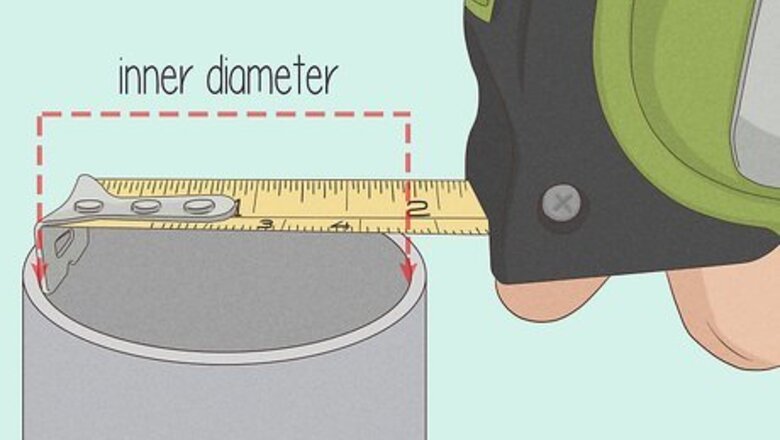
views
Using the Inside and Outside Diameters
Use a tape measure or ruler to measure the inside diameter of the pipe. Place your chosen measuring tool across the center of the pipe’s inside opening. Read the distance between the inside edge of one wall to the inside edge of the opposite wall to get the inside diameter. Make sure your ruler or tape measure is passing through the exact middle of the pipe, so that the inside edges of the wall are exactly opposite from each other. In other words, you are measuring the furthest distance across the hollow inside of the pipe. Measure using centimeters and millimeters to get the most precise measurement. Pipe wall thicknesses are usually measured using the metric system. You can use inches if you prefer.
Measure the outside diameter of the pipe using your measuring tool. Put your ruler or tape measure across the middle of the pipe’s opening. Read the distance between the outside edge of one wall to the outside edge of the opposite wall to find the outside diameter. In this step you’re measuring the furthest distance across the pipe’s opening, but from the outside of the walls instead of inside the walls.
Subtract the inside diameter from the outside diameter. Subtract the first number you got, or the smaller number, from the second number you got, or the bigger number. The difference between them is the thickness of the opposite walls combined. For example, if the outer diameter is 2 in (5.1 cm) and the inner diameter is 1.8 in (4.6 cm), subtract 1.8 in (4.6 cm) from 2 in (5.1 cm) to get 0.2 in (0.51 cm). You can do this calculation in your head or by using a calculator.
Divide the number you got by 2 to get the wall thickness. Take the number you got by subtracting the inner diameter from the outer diameter and divide it by 2 to cut it in half. The number you are left with is the pipe’s wall thickness. For example, if you got 0.2 in (0.51 cm) by subtracting the inner diameter from the outer diameter, divide 0.2 in (0.51 cm) by 2 to get a pipe wall thickness of 0.1 in (0.25 cm).
Operating an Ultrasonic Thickness Gauge
Turn on the thickness gauge by pressing the power button. Press and hold the power button. Release the power button when you see digits appear on the gauge’s display. An ultrasonic thickness gauge bounces high-frequency soundwaves through a surface to calculate the thickness of a material. You can purchase one of these gauges online for under $100 USD. Most ultrasonic thickness gauges work pretty much the same way, so you can apply this method to any make or model.
Press the CAL button to start calibrating the gauge. Press and hold the button until the screen displays CAL. This begins the gauge’s automatic calibration process. Most thickness gauges have a CAL button, but some might have an image of an old-fashioned balance instead. You can always refer to your gauge’s owner’s manual if your machine looks different and you aren’t sure how to calibrate it.
Put a dime-sized bead of ultrasound couplant gel on the sensor head. Open up a bottle of ultrasonic thickness gauge couplant gel and squeeze a generous dollop out onto the gauge’s sensor head. This gel facilitates the transmission of sound waves between the machine and the material you are measuring. The gauge’s sensor head is the round head attached to the machine’s cable. It looks kind of like a medical stethoscope. You can thickness gauge couplant gel, sometimes called coupling gel or transmission gel, online for about $15 USD or less.
Place the sensor against the calibration chip and wait for the gauge to calibrate. Press the sensor head flat against the calibration chip and hold it there steadily. Wait until the numbers on the machine’s screen stop changing. Every ultrasonic thickness gauge comes with a calibration chip that weighs a certain amount. The machine knows this number and will automatically calibrate itself to read the correct weight.
Hold the sensor head against a pipe to measure the wall thickness. Add another dime-sized dollop of couplant gel to the sensor head. Place the sensor against the outside wall of a pipe and hold it there until the numbers on the screen stop changing. The number the screen settles on is the wall thickness of the pipe in centimeters. For example, if the numbers on the screen stop changing at 0.7, the pipe’s wall thickness is 0.7 cm (0.28 in). Pipe wall thickness is usually measured using the metric system. In other words, centimeters and millimeters. However, thickness gauges also have an option to measure in inches.
Comments
0 comment