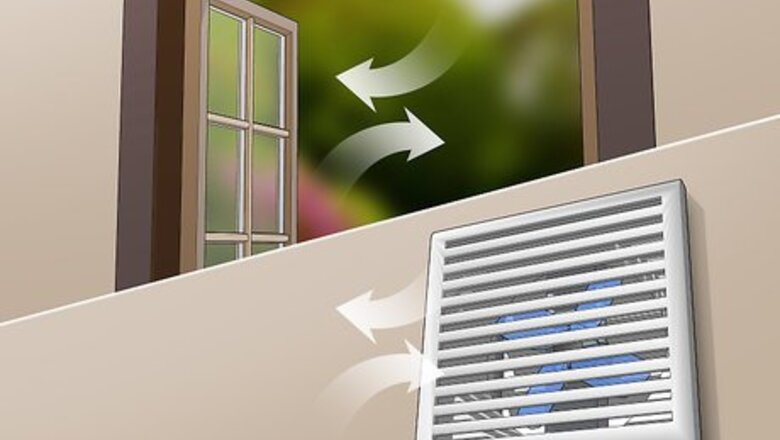
views
Cleaning and Setting up the Plastic
Set up a workspace in a ventilated area to protect against dust and fumes. Welding creates a few safety concerns to tackle before you get started. If you can, work outdoors or under a ventilation system. Open up nearby doors and windows and use fans to air out the area. Also, wear a dust mask and protective polycarbonate glasses for extra safety while preparing the plastic. Keep other people out of the area until you’re finished working.
Put on heat-resistant gloves and long-sleeved clothing for protection. You definitely need a good pair of work gloves made from a material like leather. Cover up with long-sleeved clothing, pants, and a pair of closed work boots. To protect your face, try using a clear welding visor. You don’t have to wear a full welding mask. The torches used in plastic welding don’t give off a harmful light.
Clean the plastic with soap and warm water to remove debris. Start by scrubbing off as much debris as possible with a sponge soaked in warm water. If that doesn’t work, wash the plastic with mild dish soap or detergent. Eliminate dirt, grease, and other debris the plastic picked up over time since it could weaken the weld. Then, dry the plastic off with a clean, lint-free cloth when you’re done. For stubborn stains, try using a liquid solvent called methyl ethyl ketone (MEK), which you can get online or at a hardware store. Moisten a clean rag with the solvent, then scrub the plastic until the stain comes out. Avoid using any industrial-strength detergents. They often leave behind a soapy film that affects the weld.
Use the letter identification on the plastic to choose a matching welding rod. Many plastic products often have letter identifiers printed on them. Look for the letters PE (polyethylene), PP (polypropylene), or PVC (polyvinyl chloride). Choose a rod that matches the type of plastic you plan on welding. For example, you would need a polyethylene rod to join pieces of polyethylene together. You can often fix a crack on a single piece by melting plastic around it, but have a welding rod on hand to cover any gaps.
Use a welding rod testing kit if you’re not sure what kind of plastic you have. A rod testing kit comes with all sorts of different plastic welding rods. To use the test, try to pick a rod that most closely resembles the plastic. Heat the end of the rod like you normally would in welding to attach it to a clean spot on the plastic. Then, try pulling the rod off the plastic using a pair of pliers. If it stays attached, then it is the same material as the plastic. Since you can only combine the same type of plastic, only a single rod will stay welded to the plastic. Refer to the letter marking or the test kit manual to determine what type of plastic that rod is. Testing kits, along with welding rods and other materials, are available online or at many hardware stores.
Remove paint on the plastic with a piece of 80-grit sandpaper. If the area you wish to weld has paint on it, scrub it off with rough sandpaper. Rub the sandpaper back and forth across the surface, pressing down with light but consistent pressure. Keep doing this to expose the bare plastic underneath the paint. You could also use an abrasive disc or sanding wheel that attaches to a drill. Another option is to scrape away paint with a paint scraper or another tool. Be careful not to scratch the plastic underneath the paint!
Clamp and tape plastic pieces together to hold the joint in place. Form the joint before turning on your torch. Place the plastic pieces on a bench, pushing them as close together as possible. Then, use C-clamps to pin the pieces to the table. Wrap foil tape around the pieces as needed to keep them pressed close together, but avoid covering the area you wish to weld. Make sure you secure the joints tightly and in the exact position you need. That way, you don’t have to worry about adjusting them as you focus on the weld.
Joining the Plastic
Preheat the welding gun for at least 2 minutes. Every type of plastic melts at a different temperature, so setting your welding gun up correctly is important. The temperature you need will be somewhere between 200 and 300 °C (392 and 572 °F). Anything beyond that range either burns the plastic or doesn’t melt it enough. For example, set the welding gun to 300 °C (572 °F) when working on propylene and polyurethane. Adjust the heat setting to about 275 °C (527 °F) to work on PVC. Set the heat to about 265 °C (509 °F) for polyethylene.
Secure the plastic together by tack welding the ends. Before you start the actual weld, pin loose pieces of plastic together by melting the ends of the joint. Fit a tack welding nozzle on your welding gun, then apply a little bit of heat. Wait for the plastic to begin melting, joining the pieces of plastic together. This will keep the plastic from moving as you complete the weld. A tack welding nozzle looks like a tube with a fin on the end. Press the fin against the plastic to heat it and melt it together. All you need to do is melt the plastic a little to ensure it can’t come apart. If you need to, tack weld spots every 1 ft (0.30 m) along the joint for additional security.
Trim the end of a welding rod with angle cutting pliers. Trimming a rod is very simple. Hold the pliers diagonally toward the end of the rod. Then, snip it to hone the rod to a point. If you don’t have pliers, use a trimming knife to scrape the rod to a point. By giving the rod a pointed end, you increase the chances of getting a smooth, steady weld without a big bubble of plastic where you start. You can let the welding gun cool off before changing nozzles and inserting the welding rod. However, remember to let the gun heat up again before starting the weld.
Insert a welding rod into a speed nozzle on a welding gun. A speed nozzle has an opening to hold the welding rod as you melt it onto the joint. If one didn’t come with your heat gun, you can buy one separately. After fitting the nozzle on your plastic welding heat gun, feed the rod into the second opening on top. Put the clipped end in first so you can use it when starting the weld. Make sure you don’t touch the tack nozzle if it is still hot. Either wait for the nozzle to cool or swap the nozzles carefully with a pair of pliers. With a speed nozzle, you will need to feed the rod into the opening while you weld. You could also hold the rod horizontally over the joint and melt it with a technique called pendulum welding, where you sweep the gun or torch back and forth. It takes a little longer but is great for tight spots.
Move the tip of the welding gun slowly over the plastic for a speed weld. Start at the top of the crack or area you wish to join. Hold the gun downward at about a 45-degree angle, touching the edge of the nozzle to the plastic. Then, heat the plastic until you see it beginning to melt. As you push the welding torch along the joint, feed the welding rod into it with your free hand. The key to success with welding is consistency. If you move as a deliberate pace, you can melt the plastic and welding rod just enough to bind them without burning them. If you notice the plastic burning or changing colors, move the torch at a faster pace. Don’t let it linger on the plastic or else you will end up applying too much heat.
Swing the welding gun back and forth if you’re doing a pendulum weld. Hold the nozzle about 2.54 cm (1.00 in) above the crack, tilting the gun at a 45-degree angle. Then, position the welding rod at a 45-degree angle from the opposite side. As you hold the rod in place, sweep the nozzle back and forth 3 or 4 times to melt it. Keep doing this as you move down the plastic to complete the weld. Pendulum welding is useful if you don’t have a plastic heating gun with a speed nozzle. You can do it with a basic propane torch. This is also an effective way to fill a tight joint you can’t easily reach with a speed nozzle. This part is a little trickier than with speed welds since you have to control both the torch and the welding rod at the same time. Move the torch constantly to prevent the plastic from burning. Swing it back and forth across the joint at a consistent pace to lightly heat and melt the plastic.
Finishing the Weld
Wait at least 5 minutes for the plastic to cool. Let the plastic come back to room temperature before you continue working on it. Welded plastic doesn’t take long to cool down, but you can wait as long as you please. Look for the welded plastic to turn solid. If you don’t feel any heat coming off of it, you are ready to work on it. The best time to fix a weld is before it cools. A good weld looks relatively smooth and consistent. Add more of the welding rod or smooth out the melted plastic with your gun as needed. Set your welding gun aside when you’re done. Remember to put it in a safe spot, such as in a heat-resistant holster, until it cools.
Sand the welded joint down with 120-grit sandpaper. Smooth out the rough ridges on the weld to make it look consistent with the rest of the plastic. Apply light pressure to the weld, rubbing the sandpaper back and forth across it. Try to get the weld to look level with the area around it, but be careful to avoid scratching the plastic around it. If you’re looking for a speedier way to do this, use a sanding wheel on a rotary tool. Be careful, though, since plastic is relatively soft and easy to scratch.
Finish the plastic with 180 and 320-grit sandpaper. Switch to finer grits of sandpaper to neaten out the weld. Higher-grit sandpaper is finer and less abrasive, but it can still scratch the plastic if you’re not careful. Rub the weld down like you did with the 120-grit sandpaper until it looks consistent and feels smooth to the touch. Always start with the lower-grit sandpaper. It is coarser, so it wears away more of the plastic. Save the higher-grit sandpaper for finishing.
Comments
0 comment