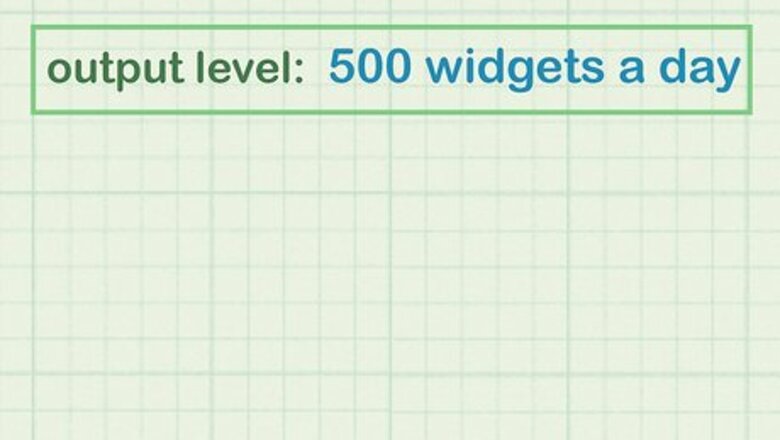
views
X
Expert Source
Alex KwanCertified Public Accountant
Expert Interview. 1 June 2021.
You may also hear marginal cost referred to as "cost of the last unit." You need to know marginal cost to maximize your profits. To calculate marginal cost, divide the change in cost by the change in quantity of the particular product or service.
Determining the Change in Quantity
Find the output level at which your fixed costs would change. To calculate marginal cost, you need to know the total cost to produce one unit of whatever product or service you sell. Fixed costs should stay the same throughout your cost analysis, so you need to find the output level at which you would have to increase those fixed expenses. For example, if you own a cupcake bakery, your ovens are a fixed expense. If your ovens are capable of baking 1,000 cupcakes a day, then 1,000 would be the maximum quantity of cupcakes you would consider for your marginal cost analysis. If you produced more than 1,000 cupcakes, your fixed costs would change because you would have to buy an additional oven.
Decide what interval you want to evaluate. You may want to calculate the marginal cost for each individual unit of the product or service you sell. However, this is generally only helpful if you produce relatively few products or services in a day. Otherwise, you probably want to look at the change in quantity as a factor of 10, 50, or even 100. For example, suppose you run a spa that gives between 3 and 5 massages a day. You want to know the marginal cost of scheduling one additional massage. In this case, it makes sense for your interval to be one.Tip: If you're having a hard time figuring out the size of the interval you want to evaluate, go with a smaller interval to start. If your marginal cost ends up being an extremely small amount, you can re-calculate using a larger interval. If you produce products, you may want to look at larger changes in quantity. For example, if your company produces 500 widgets a day, you might want to consider the marginal cost of producing 100 more, then 200 more, and so on.
Deduct the number of units in the first production run from the number of units in the second production run. Each interval constitutes a production run. To find the change in quantity, you simply subtract the old quantity from the new quantity. For example, if your company produces 500 widgets a day and you want to look at the marginal cost of producing 600 widgets a day, your change in quantity would be 100.
Pinpointing the Change in Cost
Calculate your total production costs. Your total costs consist of both fixed and variable costs for a specific number of units of a product or service. Your fixed costs are costs that do not change over the time period you're evaluating. In contrast, variable costs can be altered and may increase or decrease depending on the circumstances. Capital expenditures such as equipment would typically be fixed costs. The amount you pay each month to lease your business space would also be a fixed cost. Variable costs include your utilities, employee payroll, and the supplies that are used to produce your product or service. These costs are variable because they generally will increase as your production level increases. Calculate variable costs for each output level or production interval. Add the variable costs to the fixed costs to get your total costs.Tip: The total cost for each output level or production interval is the only number you need to calculate marginal cost. You don't need to know what portion of the total cost is fixed and what portion is variable, although this information may be valuable to you in other contexts.
Find the average cost for each unit. Once you have your total cost, you can figure out the average cost for each unit of the product or service you sell. At each output level or production interval, simply divide the total cost by the number of units. For example, if your total cost to produce 500 widgets is $500, your average total cost per unit is $1. But if your total cost to produce 600 widgets is $550, your average total cost per unit at that quantity is $0.92. You can also calculate the average fixed cost and the average variable cost.Tip: While average cost figures aren't used to calculate marginal cost, these numbers can help you find the best possible production level to maximize profits for the product or service you're selling.
Subtract the old cost from the new cost to get the change in cost. Your change in cost is measured in the same way that the change in quantity is. Deduct the costs for the smaller production interval or output level from the costs for the larger one. This amount is your change in cost for that particular interval. For example, if it costs you $500 to produce 500 widgets and $550 to produce 600 widgets, your change in cost would be $50.
Finding the Marginal Cost
Divide the change in cost by the change in quantity. The formula to calculate marginal cost is the change in cost divided by the change in quantity. So once you've figured out the change in total cost and the change in quantity, you can use these two numbers to quickly and easily calculate your marginal cost. For example, suppose you want to calculate the marginal cost of producing 600 widgets a day, up from 500 widgets a day. Your change in cost is $50 and your change in quantity is 100. Therefore your marginal cost is $0.50.
Repeat the calculation for additional intervals. Your marginal cost can increase or decrease as you continue to add additional units of production. Ultimately, you want to produce your product or service at the lowest possible marginal cost. For example, suppose your marginal cost of producing 600 widgets instead of 500 widgets is $.50. However, your marginal cost of producing an additional 100 widgets (700 widgets) is only $0.32. Producing 700 widgets would be more cost-effective than producing 500 widgets. Your marginal cost doesn't always decrease. Eventually, it will increase. For example, if you have to hire another team member to produce 800 widgets, that might increase your marginal cost to $0.52.
Enter your data on a spreadsheet to create cost curves. When you enter your data on a spreadsheet, you can create graphs that visually display the marginal costs for each production interval or output level. A marginal cost curve typically has a U-shape. The curve occurs early on in the shape, with additional units costing more to produce. Plotting your data on a curve allows you to determine what production level would be most cost-effective for your business.Tip: If you calculated your average total costs and average variable costs, you can create cost curves for these as well. They are also U-shaped curves, although the U should occur later on the line than it did for your marginal cost curve.
Comments
0 comment